Advanced Diagnostic Techniques for Industrial Equipment in Texas
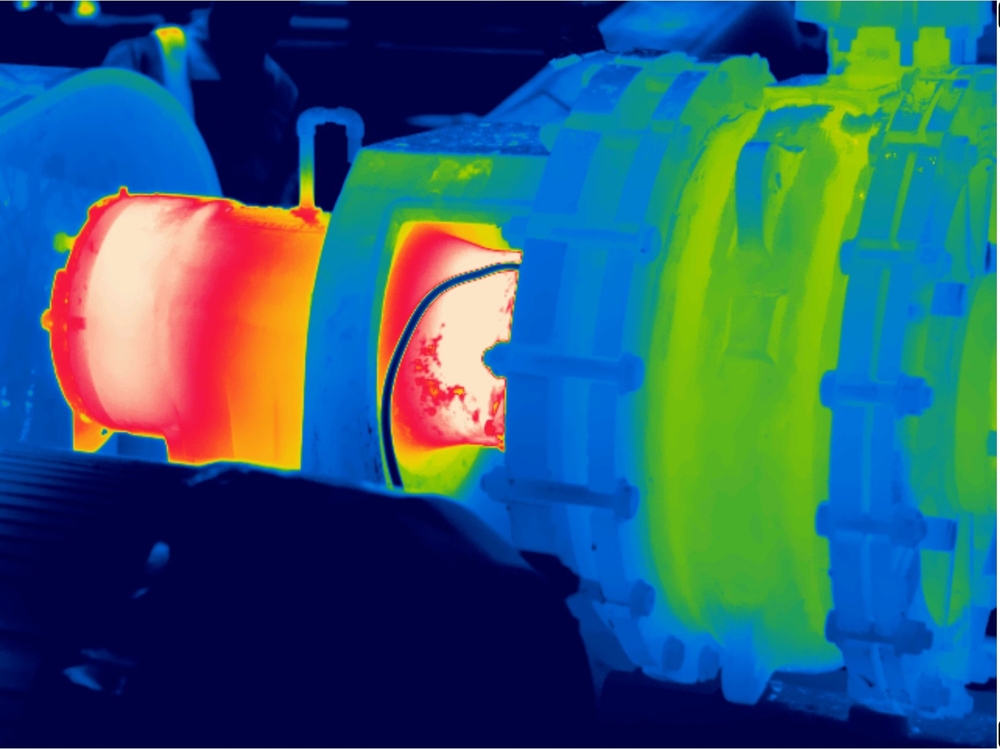
In the industrial sector, the efficiency and reliability of machinery are paramount. Industrial equipment diagnostics in Texas are crucial for maintaining optimal performance and minimizing downtime. As industries evolve, so do the methods for diagnosing and addressing equipment issues. This blog explores advanced diagnostic techniques for industrial equipment, emphasizing the importance of these methods in Texas’ diverse industrial landscape.
Understanding the Importance of Diagnostic Techniques
Industrial equipment diagnostics in Texas play a vital role in ensuring that machinery operates smoothly and efficiently. With the state’s booming industrial sector, which includes oil and gas, manufacturing, and transportation, the need for advanced diagnostic techniques has never been more critical. Proper diagnostics not only extend the lifespan of equipment but also help prevent costly breakdowns and operational disruptions.
Common Diagnostic Challenges in Industrial Settings
Complexity of Modern Equipment
Modern industrial equipment is increasingly complex, incorporating sophisticated electronics, software, and interlinked systems. This complexity can make diagnosing problems more challenging, as issues may not be immediately apparent or may require specialized knowledge to identify.
Environmental Factors
Texas is known for its diverse and often harsh environmental conditions, ranging from extreme heat to high humidity. These factors can impact the performance and longevity of industrial equipment, necessitating advanced diagnostic techniques to address and mitigate these challenges effectively.
Cost of Downtime
In industrial settings, downtime can be extremely costly. Whether it’s due to a malfunctioning pump in a manufacturing plant or a failing compressor in an oil field, any interruption in operations can lead to significant financial losses. Advanced diagnostic techniques help minimize downtime by enabling quicker and more accurate identification of issues.
Advanced Diagnostic Techniques
1. Vibration Analysis
Vibration analysis is a powerful diagnostic technique used to monitor the condition of rotating machinery. By analyzing the vibration patterns of equipment, technicians can identify issues such as misalignment, imbalance, and wear and tear. This technique is particularly useful for detecting problems before they lead to equipment failure.
How Vibration Analysis Works
Vibration sensors are installed on machinery to collect data on vibration levels. This data is then analyzed to identify abnormal patterns that may indicate potential issues. Advanced vibration analysis systems use sophisticated algorithms to provide detailed insights and predictions about equipment health.
2. Thermography
Thermography, or infrared thermography, is another advanced diagnostic technique that involves capturing and analyzing the thermal radiation emitted by equipment. By detecting temperature variations, technicians can identify hotspots and potential issues such as electrical faults, overheating components, and insulation failures.
Applications of Thermography
Thermography is commonly used for inspecting electrical panels, motors, and bearings. In Texas, where equipment often operates under extreme conditions, thermography provides valuable insights into the thermal performance and health of machinery.
3. Ultrasonic Testing
Ultrasonic testing uses high-frequency sound waves to detect flaws and anomalies within materials and equipment. This technique is particularly effective for identifying issues such as leaks, corrosion, and material degradation.
How Ultrasonic Testing Works
An ultrasonic transducer sends sound waves into the equipment, and the waves reflect off internal structures. By analyzing the reflected waves, technicians can determine the presence and location of any defects or irregularities.
4. Oil Analysis
Oil analysis involves examining the condition of lubricants used in machinery. By analyzing the properties of the oil, technicians can assess the wear and tear on equipment components and identify potential issues such as contamination or inadequate lubrication.
Benefits of Oil Analysis
Regular oil analysis helps in predicting equipment failures and scheduling maintenance before problems become critical. This proactive approach is essential for maintaining the efficiency and longevity of industrial equipment in Texas.
5. Condition Monitoring Systems
Condition monitoring systems provide real-time data on the performance and health of industrial equipment. These systems use various sensors and data acquisition technologies to continuously monitor parameters such as temperature, pressure, and vibration.
Advantages of Condition Monitoring
Condition monitoring allows for early detection of potential issues, enabling timely interventions and reducing the risk of unexpected equipment failures. In Texas, where industrial operations are often large-scale and complex, condition monitoring systems are invaluable for maintaining optimal performance.
Implementing Advanced Diagnostic Techniques in Texas
Training and Expertise
To effectively utilize advanced diagnostic techniques, it is crucial to have trained personnel with expertise in these methods. Industrial equipment diagnostics in Texas require skilled technicians who are familiar with the latest technologies and techniques.
Integration with Maintenance Programs
Advanced diagnostic techniques should be integrated into a comprehensive maintenance program. By combining diagnostics with preventive and predictive maintenance strategies, companies can ensure that their equipment remains in optimal condition and minimize the risk of unexpected failures.
Leveraging Technology
Advancements in technology, such as machine learning and data analytics, are enhancing the effectiveness of diagnostic techniques. Texas industries should stay updated with the latest technological developments to leverage these advancements for improved equipment diagnostics.
Case Studies: Success Stories in Texas
Oil and Gas Sector
In the Texas oil and gas sector, advanced diagnostic techniques have been instrumental in improving equipment reliability and reducing downtime. For example, vibration analysis and thermography have helped detect early signs of equipment failure in drilling rigs, preventing costly disruptions and ensuring continuous operations.
Manufacturing Industry
In Texas manufacturing plants, oil analysis and condition monitoring systems have played a crucial role in maintaining equipment performance. By implementing these techniques, manufacturers have been able to optimize maintenance schedules, reduce unexpected breakdowns, and enhance overall productivity.
Future Trends in Industrial Equipment Diagnostics
AI and Machine Learning
Artificial intelligence (AI) and machine learning are set to revolutionize industrial equipment diagnostics. These technologies can analyze vast amounts of data to predict equipment failures with high accuracy, enabling more proactive maintenance strategies.
Remote Diagnostics
Remote diagnostics, enabled by IoT and cloud technologies, allow technicians to monitor and diagnose equipment from anywhere. This trend is particularly relevant for industries operating in remote or challenging environments, such as those in Texas.
Enhanced Data Analytics
Enhanced data analytics tools are providing deeper insights into equipment performance and health. By integrating these tools with advanced diagnostic techniques, industries can achieve more precise and actionable insights for maintaining their equipment.
Conclusion
Advanced diagnostic techniques are essential for maintaining the efficiency and reliability of industrial equipment in Texas. By utilizing methods such as vibration analysis, thermography, ultrasonic testing, oil analysis, and condition monitoring, companies can address equipment issues proactively and minimize downtime. As technology continues to evolve, staying updated with the latest advancements will be crucial for optimizing industrial equipment diagnostics and ensuring smooth operations in Texas’ diverse industrial landscape.
Contact Us Today
Here at Kerley & Sears Inc., we understand the importance of staying ahead with advanced maintenance solutions. As a family-owned business with over 50 years of experience in the sales, service, and repair of pneumatic tools and industrial vacuum parts, we are committed to providing you with the highest level of expertise and customer service. Whether you need reliable repairs, expert advice, or a free estimate, our dedicated team is here to help. Contact us today to discover how we can support your business with our top-quality products and services.