Technological Advances in Industrial Equipment Maintenance
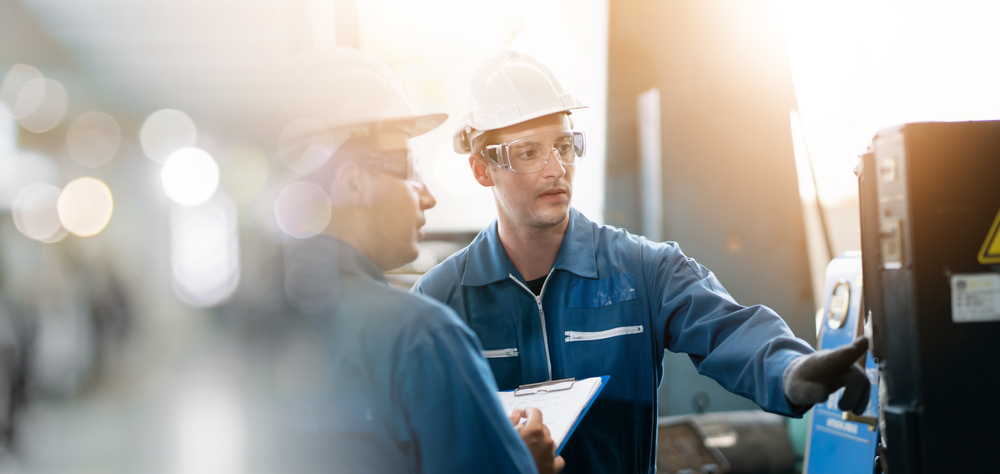
Industrial equipment plays a crucial role in modern manufacturing and production. As technology continues to evolve, so too do the methods for maintaining this equipment. In Midlothian, TX, businesses are increasingly turning to advanced maintenance solutions to ensure their machinery remains in top condition. This article explores the latest technological advancements in industrial equipment maintenance and how they are revolutionizing the industry.
The Evolution of Industrial Equipment Maintenance
Industrial equipment maintenance has traditionally been a reactive process, where issues were addressed only after they occurred. This approach, while functional, often led to costly downtime and inefficient operations. However, with the advent of new technologies, maintenance strategies have shifted towards proactive and predictive models.
From Reactive to Proactive Maintenance
Proactive maintenance involves regularly scheduled inspections and servicing to prevent equipment failures before they happen. Technological advancements have significantly enhanced this approach. For instance, advanced diagnostic tools and sensors can now monitor equipment performance in real-time, identifying potential issues before they escalate into serious problems.
Predictive Maintenance: A Game Changer
Predictive maintenance leverages data analytics and machine learning algorithms to predict when equipment is likely to fail. By analyzing historical data and real-time performance metrics, predictive maintenance can forecast potential breakdowns with impressive accuracy. This allows businesses to schedule maintenance activities at the most opportune times, minimizing downtime and reducing overall maintenance costs.
Key Technological Innovations in Equipment Maintenance
Several cutting-edge technologies are currently transforming the landscape of industrial equipment maintenance. Here are some of the most significant innovations:
Internet of Things (IoT)
The Internet of Things (IoT) is a network of interconnected devices that communicate and share data. In the context of industrial equipment maintenance, IoT sensors can be attached to machinery to collect real-time data on various parameters such as temperature, vibration, and pressure. This data is then analyzed to detect anomalies and predict potential failures. IoT technology enables continuous monitoring and immediate alerts, allowing for swift corrective actions.
Artificial Intelligence (AI) and Machine Learning
Artificial Intelligence (AI) and machine learning algorithms play a pivotal role in predictive maintenance. AI can process vast amounts of data collected from IoT sensors, identifying patterns and correlations that might be missed by human analysts. Machine learning models can continuously improve their predictive capabilities as they are exposed to more data, leading to increasingly accurate forecasts of equipment failures.
Augmented Reality (AR)
Augmented Reality (AR) is another technological advancement that is enhancing maintenance practices. AR devices, such as smart glasses or tablets, can overlay digital information onto the physical environment. This allows maintenance personnel to access real-time data, schematics, and instructions while working on equipment. AR can also facilitate remote assistance, enabling experts to guide on-site technicians through complex repair procedures from anywhere in the world.
Drones and Robotics
Drones and robotics are becoming increasingly common in industrial maintenance. Drones can be used to inspect equipment in hard-to-reach areas, capturing high-resolution images and videos that can be analyzed for signs of wear and tear. Robotics, on the other hand, can perform routine maintenance tasks with precision and consistency, reducing the need for human intervention and minimizing the risk of errors.
Benefits of Technological Advances in Maintenance
The integration of advanced technologies into industrial equipment maintenance offers numerous benefits for businesses:
Reduced Downtime
One of the most significant advantages is the reduction in equipment downtime. By predicting potential failures and addressing them before they occur, businesses can avoid unexpected breakdowns that disrupt operations. This leads to increased productivity and reduced operational costs.
Improved Equipment Longevity
Regular and accurate maintenance extends the lifespan of industrial equipment. Advanced technologies help ensure that machinery is kept in optimal condition, reducing wear and tear and preventing premature failures. As a result, businesses can maximize their return on investment in equipment.
Enhanced Safety
Technological advancements also contribute to improved safety in the workplace. Predictive maintenance and real-time monitoring help identify potential safety hazards before they become critical issues. Additionally, AR and robotics reduce the need for human personnel to work in hazardous environments, further enhancing safety.
Cost Savings
Although the initial investment in advanced maintenance technologies can be significant, the long-term cost savings are substantial. By minimizing downtime, extending equipment lifespan, and reducing the need for manual inspections and repairs, businesses can achieve considerable savings on maintenance-related expenses.
Implementing Advanced Maintenance Solutions in Midlothian, TX
For businesses in Midlothian, TX, adopting technological advances in industrial equipment maintenance can be a strategic move towards enhancing operational efficiency and competitiveness. Local maintenance solutions providers are increasingly offering cutting-edge technologies to meet the evolving needs of businesses.
Partnering with Local Experts
Collaborating with experienced maintenance solutions providers in Midlothian can help businesses integrate the latest technologies effectively. These experts can assess your equipment and recommend the most suitable technologies and strategies for your specific needs.
Investing in Training and Support
To fully leverage the benefits of advanced maintenance technologies, it is essential to invest in training for your maintenance staff. Ensuring that your team is well-versed in using new tools and techniques will maximize the effectiveness of your maintenance efforts. Additionally, ongoing support from technology providers can help address any issues that arise and keep your systems running smoothly.
Conclusion
Technological advances in industrial equipment maintenance are transforming the way businesses approach machinery upkeep. From predictive maintenance and IoT to AI, AR, and robotics, these innovations are driving significant improvements in efficiency, safety, and cost-effectiveness. For businesses in Midlothian, TX, embracing these advancements can lead to enhanced operational performance and a competitive edge in the market. By partnering with local maintenance solutions providers and investing in training and support, businesses can ensure they make the most of these cutting-edge technologies.
Contact Us Today
Here at Kerley & Sears Inc., we understand the importance of staying ahead with advanced maintenance solutions. As a family-owned business with over 50 years of experience in the sales, service, and repair of pneumatic tools and industrial vacuum parts, we are committed to providing you with the highest level of expertise and customer service. Whether you need reliable repairs, expert advice, or a free estimate, our dedicated team is here to help. Contact us today to discover how we can support your business with our top-quality products and services.