How to Optimize Your Industrial Lubrication Systems
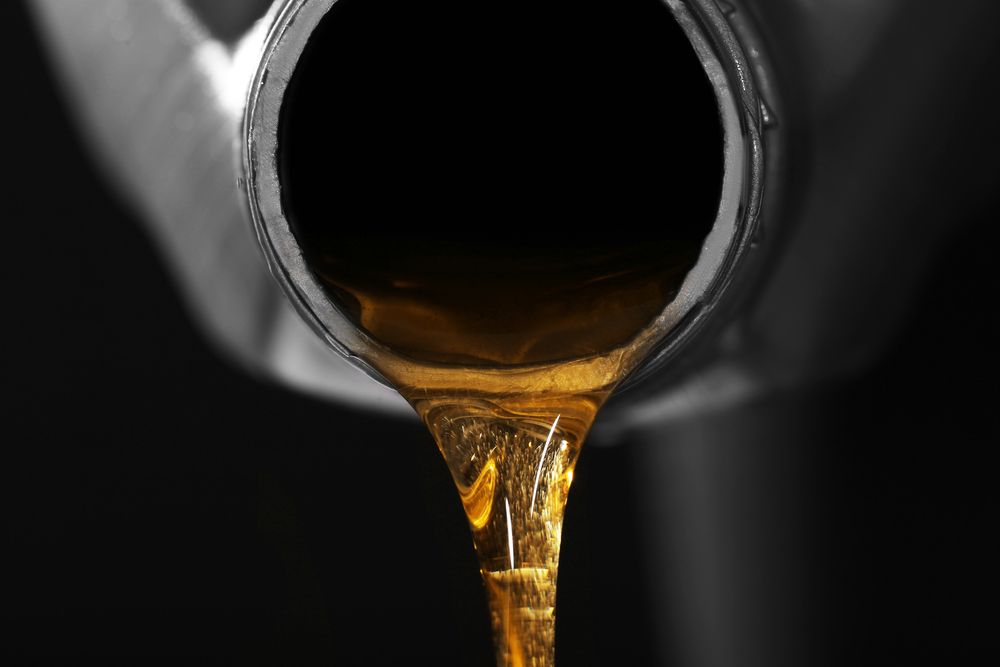
Industrial lubrication systems play a crucial role in maintaining the efficiency and longevity of machinery across various sectors. Whether you operate in manufacturing, mining, or transportation, optimizing your lubrication processes is essential for minimizing downtime, reducing maintenance costs, and enhancing overall productivity. Here’s a comprehensive guide on how you can effectively manage and optimize your industrial lubrication systems.
Understanding Industrial Lubrication Systems
Industrial lubrication systems are designed to reduce friction between moving parts within machinery, thereby preventing wear and tear. These systems utilize various lubricants such as oils, greases, and fluids to ensure smooth operation and extend the lifespan of equipment. Proper lubrication not only improves operational efficiency but also enhances safety by reducing the risk of equipment failure.
Importance of Optimal Lubrication
Optimizing your industrial lubrication systems offers several benefits, including:
- Enhanced Equipment Performance: Proper lubrication reduces friction, which in turn improves machinery performance and energy efficiency.
- Extended Equipment Lifespan: Regular lubrication maintenance prevents premature wear and prolongs the life of critical components.
- Cost Savings: Effective lubrication practices can lower maintenance costs associated with repairs and replacements.
Steps to Optimize Industrial Lubrication Systems
1. Conduct a Comprehensive Assessment
Begin by conducting a thorough assessment of your current lubrication practices. Identify equipment that requires lubrication and evaluate the type and frequency of lubrication currently employed. This assessment helps in understanding any existing inefficiencies or areas for improvement.
2. Choose the Right Lubricants
Selecting the appropriate lubricants is crucial for optimizing your lubrication system. Consider factors such as equipment type, operating conditions, temperature variations, and load capacities when choosing between oils, greases, or specialty lubricants. Opt for high-quality products that meet manufacturer specifications to ensure optimal performance.
3. Implement a Regular Maintenance Schedule
Establishing a proactive maintenance schedule is key to optimizing industrial lubrication systems. Create a calendar for lubrication tasks based on equipment usage and manufacturer recommendations. Regularly inspect and replenish lubricants, and monitor equipment performance to detect any signs of wear or lubrication issues promptly.
4. Utilize Automated Lubrication Systems
Investing in automated lubrication systems can streamline maintenance processes and ensure consistent lubrication across machinery. These systems can be programmed to deliver precise amounts of lubricant at scheduled intervals, reducing human error and optimizing lubrication efficiency.
5. Train Maintenance Personnel
Provide adequate training to maintenance personnel responsible for lubrication tasks. Ensure they understand the importance of proper lubrication techniques, safety protocols, and equipment-specific requirements. Well-trained staff can identify potential issues early on and perform lubrication tasks effectively.
6. Monitor Performance and Efficiency
Implement monitoring systems to track lubrication performance and equipment efficiency. Utilize sensors, gauges, or condition monitoring technologies to measure lubricant levels, temperature, and vibration. Analyzing data from these systems allows for proactive maintenance and adjustments to optimize lubrication processes further.
Conclusion
Effectively optimizing your industrial lubrication systems requires a strategic approach encompassing assessment, selection of appropriate lubricants, regular maintenance, utilization of automated systems, training of personnel, and continuous performance monitoring. By implementing these steps, businesses can enhance equipment performance, extend lifespan, and achieve significant cost savings in maintenance and repairs. Investing in optimal lubrication practices not only improves operational efficiency but also contributes to overall safety and sustainability in industrial operations.
Contact Us Today
Here at Kerley & Sears Inc., we understand the pivotal role that efficient lubrication systems play in your industrial operations. Our team of experts is ready to help you optimize your lubrication processes, ensuring your machinery runs smoothly and efficiently. Reach out to us today to schedule a consultation and discover how our tailored solutions can reduce downtime, cut maintenance costs, and enhance your overall productivity. Let us partner with you in maximizing the performance and longevity of your equipment.